Efficient Carbon Removal with Ultrasonic Cleaning: Best Solutions and Practices
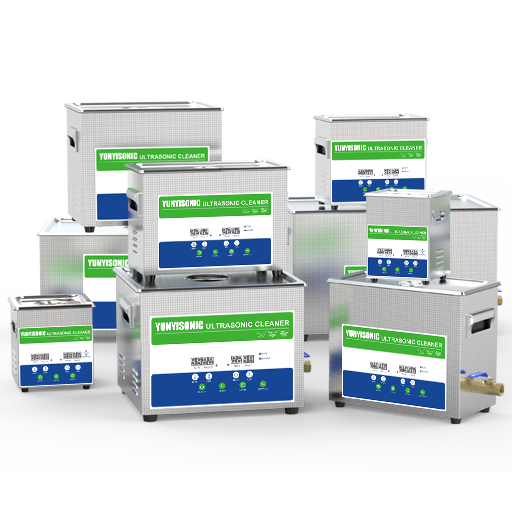
Carbon deposits are a persistent challenge in the maintenance of engine parts, injection molds, fuel systems, and machined components. Traditional cleaning methods—such as manual scraping, chemical soaking, or high-temperature burning—are not only time-consuming and abrasive but also pose safety and environmental hazards. By contrast, ultrasonic cleaning technology offers a safer, faster, and more effective method for carbon removal, particularly when paired with the right cleaning solution.
1. Why Use Ultrasonic Technology for Carbon Removal?
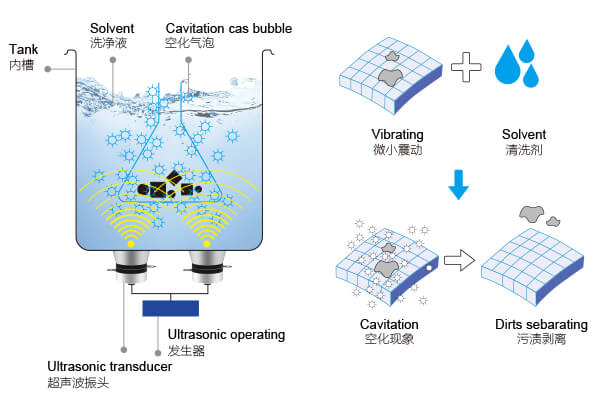
The Principle Behind Ultrasonic Cleaning
Deep Penetration via Cavitation
Ultrasonic cleaners operate by creating high-frequency sound waves in liquid, generating microscopic cavitation bubbles that collapse and release energy. This effect physically dislodges carbon buildup—even in hard-to-reach crevices and interior passages—without needing aggressive chemicals or physical force.
Non-Destructive Cleaning
Ultrasonic cleaning is gentle on sensitive components like aluminum, copper, or precision steel. Unlike scrubbing or acid immersion, it preserves the integrity of engine blocks, injectors, and machined surfaces.
Fast, Environmentally Safer Results
When combined with the appropriate carbon-removing solution, ultrasonic cleaning can achieve results in minutes that traditionally required hours. Additionally, it minimizes VOC emissions and chemical runoff, contributing to a safer workspace and greener operations.
2. Recommended Cleaning Solutions for Carbon in Ultrasonic Systems
The efficiency of ultrasonic carbon removal depends heavily on the cleaning solution used. Here are three main categories:
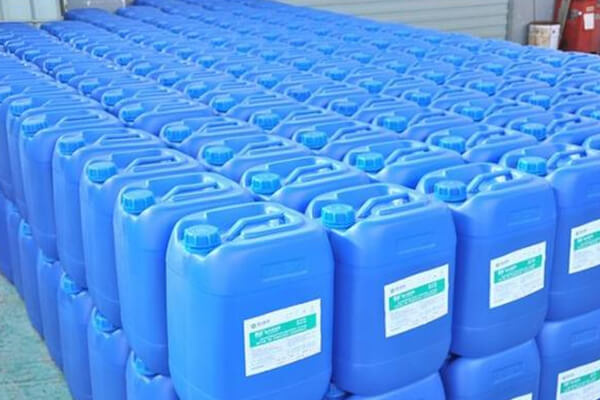
Ultrasonic cleaning machine cleaning fluid
1. Alkaline Carbon Removers
Formulated with sodium hydroxide or potassium carbonate, these are ideal for heavy carbon on steel parts like injectors and valve bodies. They work by softening hardened deposits, allowing ultrasonic cavitation to dislodge contaminants more effectively, even in dense build-up areas.
- Use: 5–10% concentration at 60–70°C
- Note: Avoid on aluminum without corrosion inhibitors
2. Degreasing Penetrant Solutions
Combining surfactants and penetrants, these break down oily carbon layers on non-ferrous metals. They help dissolve stubborn residues in tight spaces, making them ideal for precision parts and intricate geometries.
- Use: Neutral to mildly alkaline pH
- Best for: Aluminum, copper, and alloy parts
- Cycle time: 10–15 minutes
3. Recommended Ultrasonic Cleaning Parameters for Carbon Removal
Cleaning performance depends not only on the fluid but also on how the machine is used:
- Ultrasonic Frequency:
- Temperature: 60°C–70°C accelerates carbon softening; avoid overheating with sensitive alloys.
- Time:
- Light carbon: 5–8 minutes
- Medium: 10–15 minutes
- Heavy/baked carbon: 20+ minutes or multiple cycles with fresh solution
4. Real-World Case Studies and Results
Auto Shop Engine Block Cleaning
At a high-volume automotive repair center, technicians used a 10% alkaline carbon removal solution at 60°C with a 30kHz ultrasonic setting to clean cylinder heads and intake valves. After 15 minutes, hardened carbon deposits—including those in narrow oil passages—were significantly loosened and removed with minimal brushing. This process not only cut cleaning time by more than 60% but also improved overall workshop throughput and reduced labor fatigue.
Injection Mold Burnt Residue Removal
In a plastics manufacturing plant, injection molds often accumulate carbonized residues and oxidized polymers that impact mold precision and cycle efficiency. Using a weak alkaline degreaser in a 50kHz ultrasonic cleaner set to 65°C, technicians completed cleaning in 12 minutes. The process restored cavity definition without compromising metal tolerances or inducing heat stress. Mold lifespan increased by an estimated 20% due to the non-destructive cleaning process.
Laboratory Valve and Microcomponent Cleaning
A research lab faced challenges in cleaning miniature valves and sensor housings used in gas chromatography. Carbon residues were embedded deep within millimeter-scale channels. Using an enzyme-based biodegradable solution at 55°C with an 80kHz ultrasonic frequency, the lab achieved a complete clean in 20 minutes without the need to dismantle the components. Post-cleaning testing confirmed no residual contamination, and parts were immediately reusable in precision applications.
Diesel Injector Reconditioning Facility
At a diesel injector refurbishing site, technicians often struggled with layered carbon, varnish, and diesel residues. A dual-phase cleaning protocol was adopted: first using a degreasing solution at 40kHz and 60°C for 10 minutes, followed by a stronger alkaline rinse at 30kHz for another 10 minutes. This two-step ultrasonic approach restored fuel flow rates to 95%+ of original specifications, reducing warranty claims and boosting customer satisfaction.
Aerospace Maintenance Workshop
Carbon fouling inside turbine nozzle guide vanes and fuel nozzles was traditionally removed using mechanical scraping and solvent soaking. Switching to a tailored ultrasonic cleaning setup using a pH-neutral solution with corrosion inhibitors, operators cleaned components in a 28/68kHz dual-frequency unit at 65°C. Cleaning time was reduced by half, and structural integrity remained uncompromised. The non-abrasive process met strict aerospace part reuse standards.
Automotive Remanufacturing Line – EGR Valve Cleaning
Exhaust Gas Recirculation (EGR) valves notoriously trap soot and carbon over time. A remanufacturing facility integrated a 40kHz ultrasonic cleaner with a high-efficiency carbon solvent at 65°C. A 12-minute cycle followed by a rinse ensured carbon removal even from interior pathways. Post-clean inspections showed zero residual buildup, and component throughput increased by 30% compared to manual methods.
5. Maintenance Tips and Common Mistakes
To ensure consistent performance and equipment longevity:
-
baskets
Change Cleaning Fluid Regularly
Used fluid accumulates dissolved carbon and loses efficacy. Replace every 3–5 cycles or as soon as it becomes visibly dirty. - Avoid Harsh Chemicals
Strong acids may provide quick results but can damage equipment and workpieces over time. - Use Proper Baskets and Racks
Never place items directly on the tank bottom—this causes uneven cleaning and can damage both the items and transducers. - Monitor Temperature and Power
Overheating or running continuously without rest can wear down components. Follow recommended duty cycles. - Ensure Good Ventilation
Even safe solutions may release vapors during heating—use in a well-ventilated space and wear protective gloves.
Modern Carbon Cleaning, Smarter and Greener
As industries move toward smarter and cleaner technologies, ultrasonic carbon removal has become a cornerstone of modern maintenance and production workflows. With the right cleaning fluids and operating parameters, users can eliminate stubborn deposits quickly and safely—without sacrificing part integrity or sustainability.
From engine shops to laboratories, ultrasonic cleaning is proving to be a powerful and eco-friendly alternative to outdated, hazardous methods. When done right, it’s not just cleaning—it’s precision restoration with environmental responsibility in mind.
In the field of ultrasonic carbon removal, Yunyisonic ultrasonic cleaners stand out with exceptional performance, versatility, and reliability. Backed by strong R&D capabilities and years of specialized manufacturing experience, Yunyisonic delivers high-efficiency cleaning solutions tailored for everything from heavy carbon buildup on engine components to delicate lab-scale instruments.
What sets Yunyisonic apart is its comprehensive frequency coverage and customizable configurations. With dual-frequency silent systems, and triple-frequency units and four-frequency designed for multi-phase cleaning, Yunyisonic ensures optimal cavitation strength and precision for any contamination level—from thick baked-on carbon to fine soot lodged in complex geometries.
Moreover, Yunyisonic’s machines are engineered with user-centric controls, durable materials, and strict quality assurance, making them ideal for demanding environments such as automotive remanufacturing, aerospace maintenance, and scientific research. The company’s ability to offer bespoke multi-frequency solutions further enhances its edge in tackling the most challenging carbon cleaning tasks.
Trusted in over 100 countries, Yunyisonic continues to redefine what’s possible in ultrasonic cleaning—helping industries achieve deeper, faster, and safer carbon removal with every cycle.